12 ways to manage electrical risks in your workplace
As the numbers of electrical safety incidents increase across Australia, as reported by the safety regulators, persons conducting a business or undertaking (PCBUs) must remain vigilant in ensuring that electrical risks are eliminated from their operations, so far as reasonably practicable.
General duty to manage electrical risks
A risk of serious injury or death can occur if a person comes into contact with exposed live wires or equipment or where electricity causes a fire or explosion. The risk is particularly heightened in outdoor or wet conditions, or in confined spaces.
Damaged equipment can also pose hazards. A PCBU with management or control over electrical equipment, including an electrical installation, must ensure, so far as reasonably practicable, that the equipment is safe to use.
What should you do?
There are a range of controls that can be put in place to manage electrical risks. One of the challenges is often identifying where the risk exists, particularly in a changing work environment such as a construction site.
Your business should review its work practices and identify where these risks currently exist or may arise in future activities that will be undertaken. Once that step is taken, consider the SafeWork NSW checklist, which lists the following controls that could be put in place:
- Ensure only appropriately licensed or registered electricians carry out electrical work.
- Provide safe and suitable electrical equipment, e.g. not using leads and tools in damp or wet conditions unless they are specially designed for those conditions.
- Inspect leads for damage before use and remove any that are damaged from the workplace.
- Provide enough socket outlets. Overloading socket outlets by using adaptors can cause fires.
- Ensure power circuits are protected by the appropriate rated fuse or circuit breaker to prevent overloading.
- If the circuit keeps overloading, don’t increase the fuse rating, as this creates a fire risk due to overheating.
- Use battery-powered tools instead of mains-operated, where possible.
- So far as reasonably practicable, arrange electrical leads so they will not be damaged. You can do this by not running leads across the floor or ground, through doorways and over sharp edges; using lead stands or insulated cable hangers to keep leads off the ground; using cable protection ramps or covers to protect cables and cords, where applicable.
- Use residual current devices (RCDs) (also known as safety switches) to protect workers using portable equipment, as required by the Work Health and Safety Regulation.
- Determine the reason why an RCD, circuit breaker or other over current protective device disconnected the electricity before it is switched back on.
- Ensure RCDs are effective by regular testing.
- Carry out preventative maintenance on electrical equipment as appropriate for example an appropriate system of visual inspection and where necessary, testing.
Find out more
For more information about managing electrical risks in your workplace, review the Health & Safety Handbook chapter, Electrical safety.
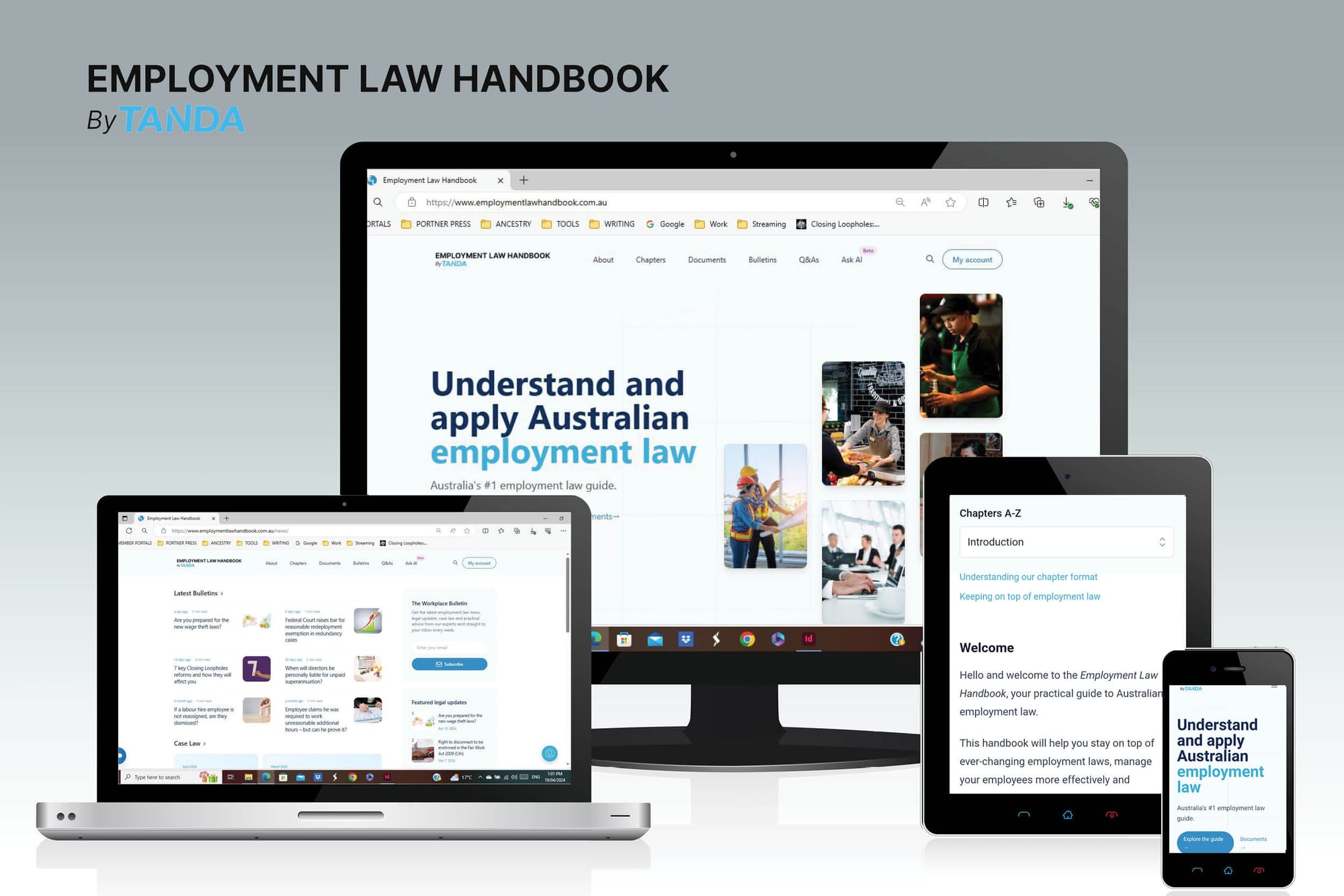
From the experts behind the Health & Safety Handbook, the Bulletin brings you the latest work health and safety news, legal updates, case law and practical advice straight to your inbox every week.